The printing sector has been expanding lately, and many businesses are switching to DTF printing. So, what is DTF (Direct to Film) printing? DTF printing is a technique that allows for versatile and cost-effective printing solutions, making it a preferred choice for many businesses in the modern printing era. DTF Printer offers performance consistency, ease of use, and an extensive color range.
Furthermore, owning a DTF printer is now a dependable and economical investment. DTF printing involves directly transferring ink from the film onto the substrate, offering vibrant and durable prints. With DTF printing, businesses can achieve high-quality results on various materials, including garments and textiles.
Let’s get right into it and see what a direct-to-film Printer can accomplish for you.
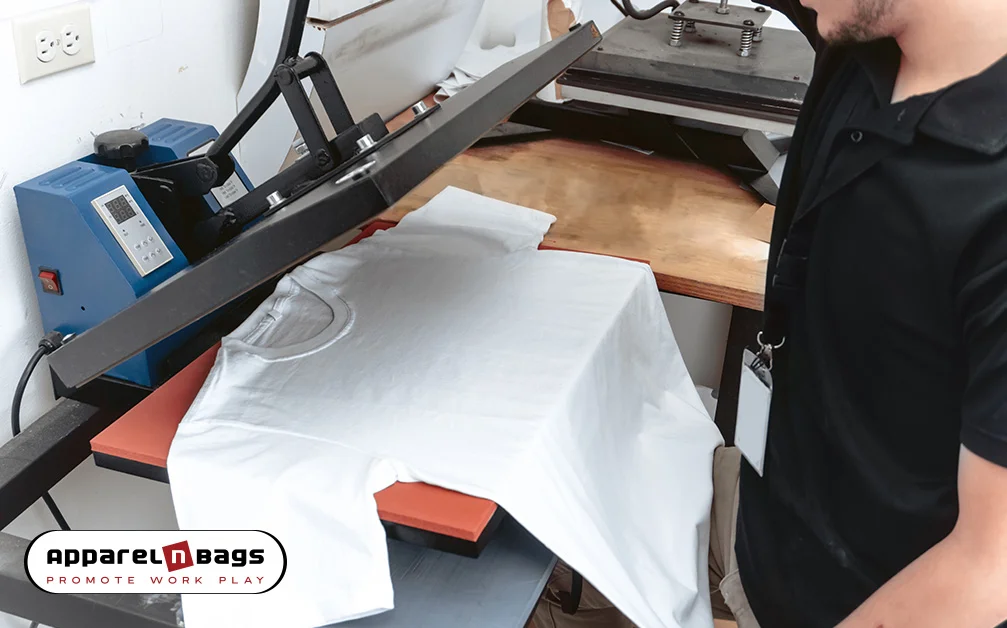
Let’s learn “What is DTF printing?” It is an inventive method of heat-transfer-based . A heat press prints designs to the final substrate using dye or pigment-based ink on a transparent film coated with hot-melt adhesive powder to transfer them to the final substrate.
DTF printers are designed for high-volume production and start at more than $15,000. For this kind of transfer, powdered adhesive must be applied by hand or shaker equipment. Certain DTF printers include shakers, but others do not, and this could cost you extra.
This approach’s huge benefit is that the white ink layer and the colored ink are printed simultaneously. Compared to other techniques, like using white toner, this property makes it a reasonably straightforward substitute.
When working with DTF, you should know that the following file types—EPS, PS, PDF, BMP, TIF, JPG, PNG, and PSD—can print your designs.
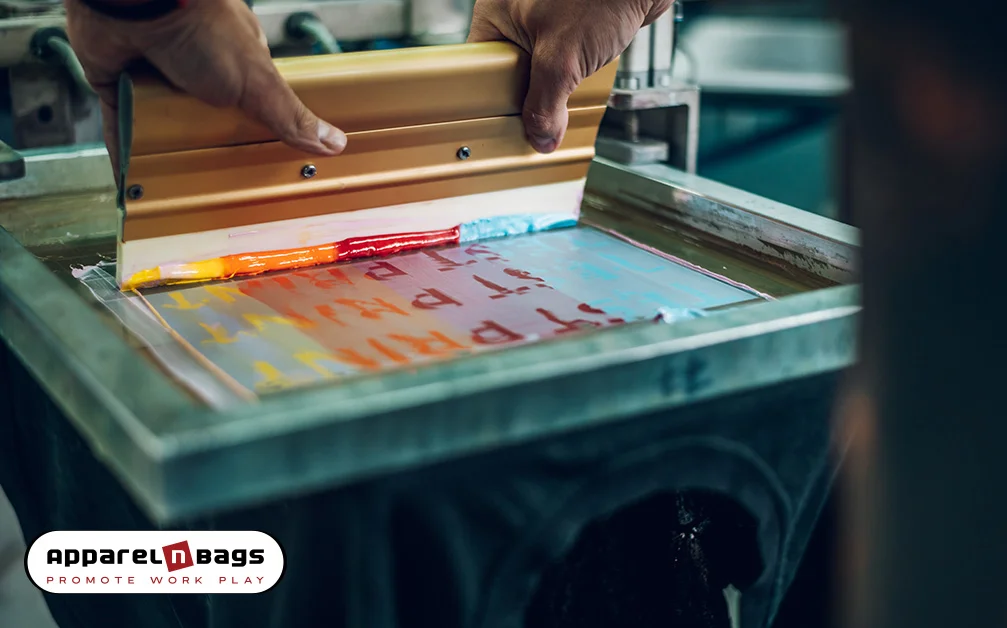
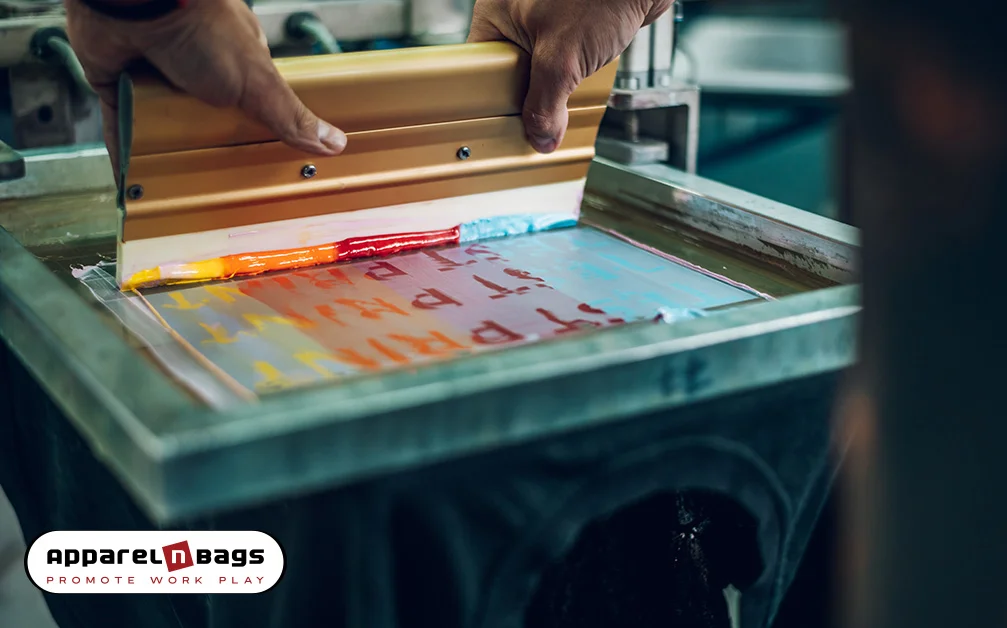
Step 1: Film and Powder Adhesive Preparation
The complete design is printed in color on a PET film and fed into the DTF printing device.
Following the creation of the first layer, the machine prints a white layer across the whole image, completely covering the layer.
The wet ink is then evenly covered with a sticky powder. The excessive powder is removed before heating the film for fabric transfer. A heat press machine or a curing oven is used for adhesive heating.
Step 2: Fabric Pre-Pressing and Heat-Pressing
The cloth that is to be printed is heated for two to five seconds in the heat press machine to dehumidify and pre-flatten it. Meanwhile, the PET film has also been preheated.
After the first flattening, the film is placed on the pre-pressed fabric. Afterward, a heat press is used to transfer the film’s design to the garment by pressing it for 15 to 20 seconds at an average temperature of 165°C.
Step 3: Load the Film
Put a transparent DTF film into the printer. Verify that the film is firmly positioned and aligned.
Step 4: Print the layout
Send the design file to the DTF printer to start the printing process. The printer will print the design on the translucent film.
Step 5: Utilize the Adhesive Powder:
After printing the design, gently remove the film from the printer and place it on a level surface. To assure complete coverage, uniformly apply a layer of adhesive powder over the whole printed area of t-shirts.
Step 6: Shake Off Extra Powder
To remove the extra adhesive powder, gently shake the film. The powder will only stick to the printed design over different Colors.
Step 7: Cure the Adhesive
Heat the adhesive powder onto the film using a heat press machine or a specialist curing device. This will cause the adhesive to become active and stick to the different design.
Step 8: Transfer the Design
If you wish to transfer the design, place the film and adhesive side down on the custom sweatshirts. Make sure it is appropriately positioned and apply pressure to the substrate.
Step 9: Apply Heat and Pressure
Heat and pressure should be applied to the film and custom sweatshirts using a heat press machine. Sweatshirt slub fabric will be bonded to the design as the adhesive melts due to the heat.
Step 10: Post-Processing
Depending on the particular specifications of your print, you need to understand how to stretch a t-shirts. Take extra measures like applying protective coatings or curing the print again for increased longevity.
You may be wondering what tools you’ll need to make your garments distinct with DTF printing.
Here’s What You’ll Require
Let’s begin by listing the tools and machines you will require:
- An inkjet printer modified for DTF printing with six ink channels CMYK+White: Find an inkjet printer that is modified to work as DTF printer with all the necessary hardware alterations.
- Special inks for DTF printing: Elastic inkjet inks that
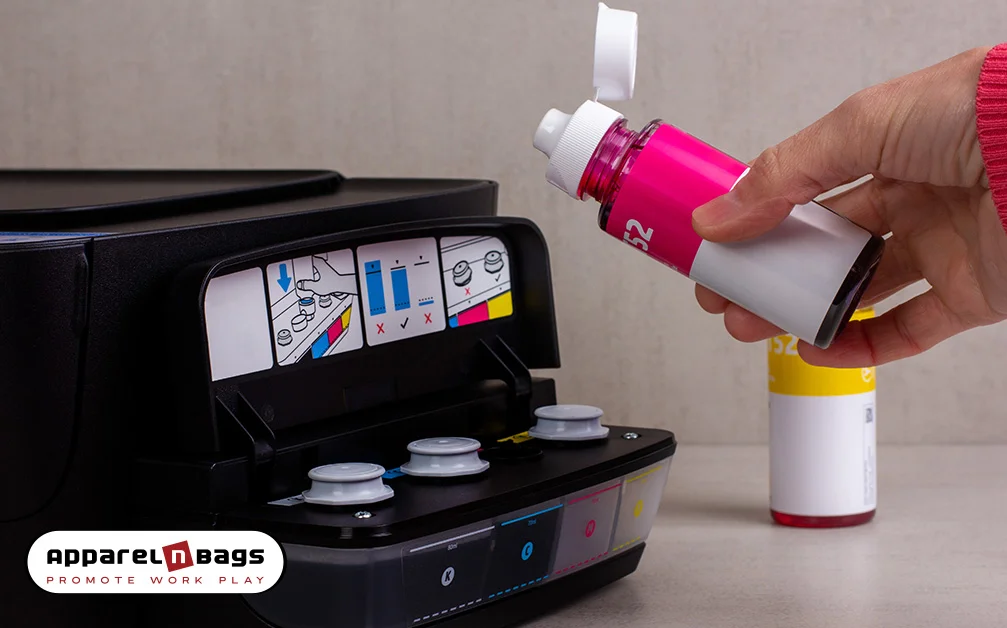
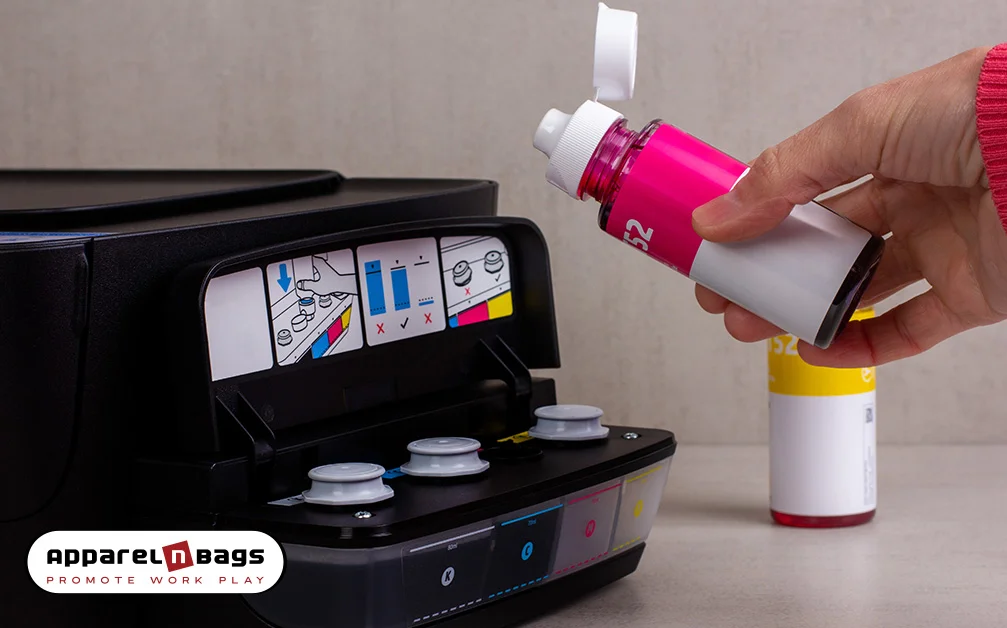
prevent the print from cracking when stretching the garment after printing .
- DTF film: It’s the surface on which you print your design.
- DTF powder: It acts as an adhesive between the inks and the cotton fibers.
- RIP software: This software is necessary to print CMYK and white-colored layers correctly because, as mentioned before, the printer has been modified and cannot print in the correct order by itself.
- Heat press: We recommend a press with an upper platen that lowers vertically to make the DTF film’s curing process easier.
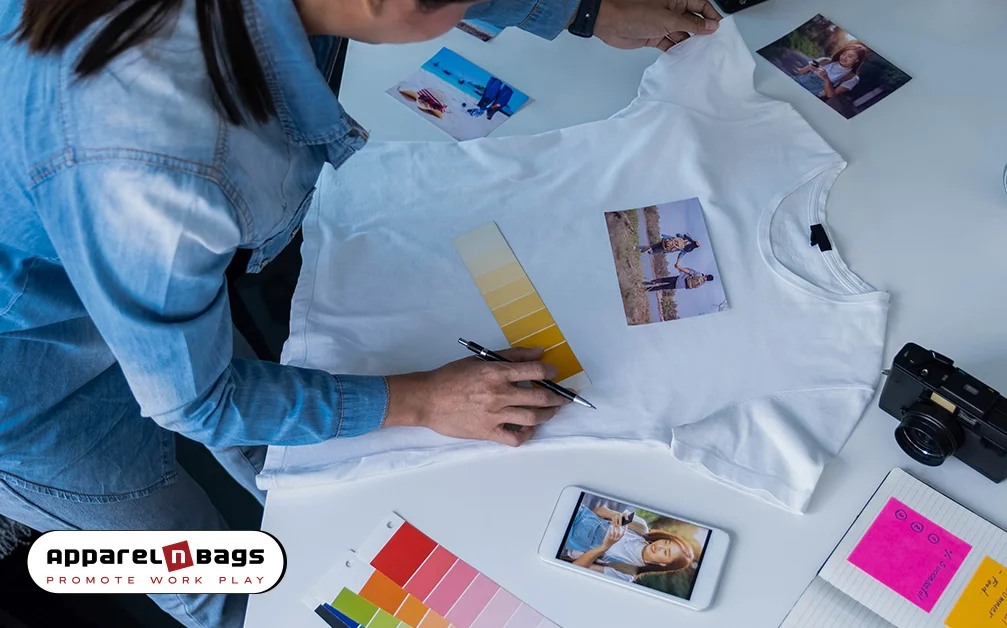
So, is a Direct-to-Film Printer a wise purchase? Let’s start by analyzing the pros and cons of this revolutionary advancement in printing technology.
Pros
- Nothing unusual needs to be prepared for it.
- It can be used on a broad range of textiles and materials because of its versatility.
- The texture of the material as it was originally printed may still be slightly noticeable. However, once printed, the cloth will exhibit excellent resistance to washing.
- This printing technology can be implemented more quickly and easily than others, such as
Cons
- The printed area is marginally more noticeable than with subliminal printing.
- The colors could be more vibrant with sublimation printing.
Differences Between DTF, DTG and White Toner Printing
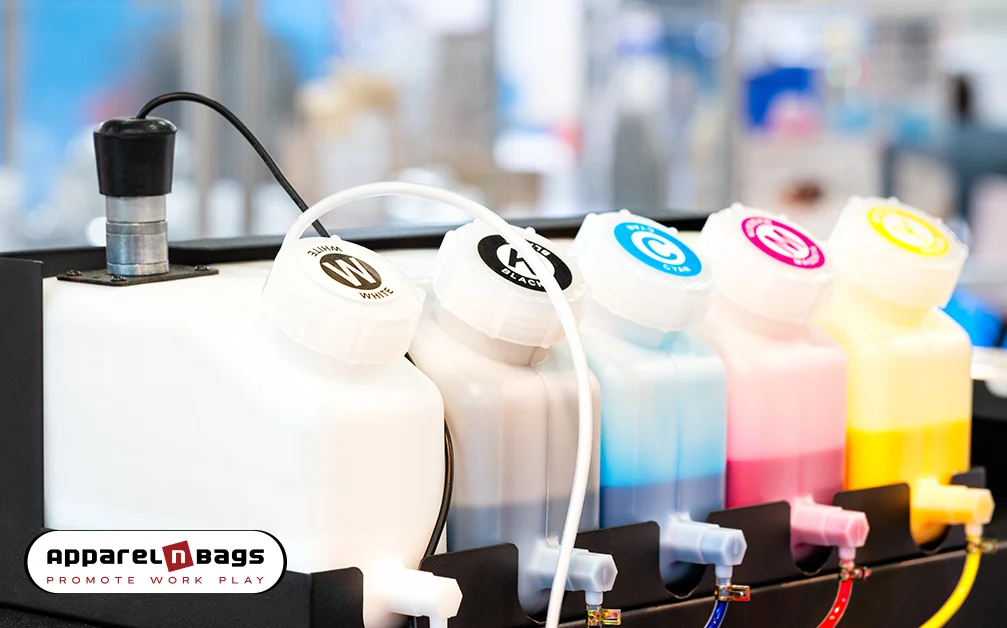
DTF printing and DTG printing with white toner share conceptual similarities, making comparisons difficult. Let’s examine the differences between these techniques so that you may select the approach that is most effective for you.
Comparing DTG and DTF Printing
DTF and DTG are similar in that both need white ink in an inkjet printer. What specific differences exist between them?
- DTF printing is a less expensive option than direct-to-garment printing, as the DTF kit is significantly less costly.
- The first step in the production process for DTF printing is printing a design onto a film. Next, you must incorporate the DTF powder. Once the printed film has cured, the pattern can be transferred to the fabric. Unlike DTG printing that does not require intermediary substrates and significantly reduces manufacturing time.
- Regarding feel and appearance, DTF has a slightly “plastic” finish strikingly comparable to screen printing. However, because the inks are so elastic, even if the clothing is stretched, the print doesn’t chip. On the other hand, because the ink is completely absorbed into the garment during direct-to-garment (DTG) printing, the result is a smoother finish and a more flawless appearance.
- DTG printing produces a whiter, purer color, while white loses part of its clarity and brilliance while when with DTF.
- Both techniques are light on the pocket because of a cheap cost of production. The cost of a t-shirts printed with this DTF method is less than that of a t-shirt made with the direct-to-garment (DTG) printing method, though the DTF printing process requires more materials.
DTF vs. White Toner Printing
- The two processes are similar Since printing the design is necessary for t-shirts transfer. The finished result has a similar texture as well. To produce customized t-shirts, let’s compare the quality of DTF printing to that of inexpensive white toner.
- A DTF kit requires less money upfront than a laser printer. It costs about half as much as a laser printer from OKI or Uninet.
- Compared to low-cost white toner systems, DTF is more straightforward because the white layer prints alongside the color layer the entire time.
- The two printing techniques have almost the same texture and feel. Since DTF inks are textile inks, they are more pliable and stain-resistant.
- White toner enhances two qualities of white color: purity and brightness.
- White toner printing is far more expensive than direct-to-fabric (DTF) printing since it requires toner and NO CUT transfer sheets. Using a DTF printer to produce a customized t-shirt is 50% less expensive than using white toner to make the same t-shirt.
- White toner laser printing works well for many applications. However, direct-to-film printing (DTF) is best suited for textiles. In addition to this category of items, colorful rigid item modification is also a choice.
Recognizing and Fixing Issues with Ink Adhesion
Problem #1: Inadequate ink adherence, resulting in smearing or flaking.
Solution #1:
- Check the heat and pressure settings for adequate curing.
- Refrain from destroying Jerzees 29L by using the suggested ink and substrate combinations.
If necessary, pretreat substrates to improve ink adhesion.
Problem #2: Ink leaking or dispersing outside the intended print region.
Solution #2: Assess the ink’s viscosity and make necessary adjustments. Make sure the printed layers are properly dried between them. Use the proper print settings to manage ink flow.
Dealing with Image Quality
The first Problem is blurry printouts.
First solution: Verify print resolution and make necessary adjustments for best clarity. Make sure the t-shirt are positioned correctly and are flat. Regular maintenance and cleaning of the printer heads are essential.
The second Problem is uneven or inaccurate color reproduction.
The second solution is to calibrate the printer so that the t-shirt gets accurate colors. Use profiles and color management software and verify ink levels and swap out cartridges as necessary.
Maintaining and Calibrating DTF Printers for Optimal Performance.
Problem#1 is printer jams or misfeeds
First solution: Make sure the printer rollers are clean and free of debris. Modify the orientation of the film or paper. Use the appropriate tension settings for easy feeding.
Problem #2: Prints with uneven ink distribution or banding.
Second solution: Carry out routine upkeep, such as clearing the print heads and ensuring the ink flows unhindered. Calibrate the printer to ensure equal ink distribution throughout the t-shirts.
Problem #3: Problems with printers or mistakes in them
Third solution: Update printer drivers and firmware as the third solution. If necessary, reset the printer and do a power cycle. Ink all over the body could damage t-shirt if this Problem is not fixed. For additional support, get in touch with ApparelnBags technical support.
Routine maintenance, proper calibration, and following manufacturer’s instructions can help minimize ink bleeding over different t-shirts. Additionally, it can fix common DTF printing problems. Depending on the ink system and printer model, different troubleshooting methods may be used.